
The most common reason models become unprintable is due to bad objects and naked edges.īad Object: Objects that violate NURBS rules or have structural problems.
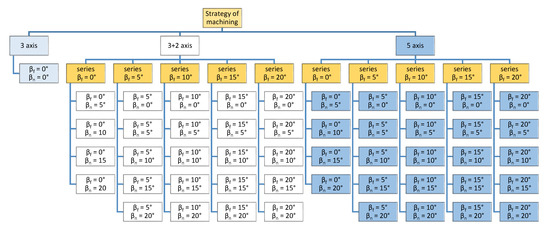
To achieve a watertight model, you need a closed polysurface. if you dropped the model in a bath, no water would leak inside. Check Your 3D Modelsįor successful 3D prints, the 3D model should be watertight, i.e. Make sure your units are set to mm before exporting your file for printing. No matter what units you use to create your model, files exported from Rhino are almost always read as mm. Rhino file tolerance can be set from the document properties window, units tab. Set correct tolerances before you start modelling by finding the tolerance of the program you are exporting your model to and setting Rhino tolerance to be 10 times that (i.e., printer tolerance is 0.1mm, so Rhino tolerance should be set to 0.01mm).
Stl tolerance mastercam 2019 how to#
There are some unique considerations to keep in mind when preparing 3D print files specifically in Rhino, so for this post, we’re going to go into more detail on how to export your CAD models here. So the key thing when doing multiple operations in one file is to not flip the part but rather use a new plane for each operation.We recently wrote an overview on How to Prepare CAD Files for 3D Printing, going over some general considerations and steps to properly export your 3D printing files. That sounds easy enough, Your not actually flipping the part though right? as long as you don't actually flip the part, use the same part or solid for all 4 ops and use planes to flip the part. We machine one off parts to parts in the tens of thousands for a decade long but always need to be as efficient as possible. My issue is going from one Op to the next op, keep flipping the job over and using the same stock reference. Op 4: Flip back over and 3d finish the outside here on a custom nest fixture I also need to create. Op 3: flip it back over, finish inside pocket first from this side, and then finish ouside 3d possible from this side. Op 2: flip it over, rough out stock and finish inside pocket where possible.

Op 1: setup, square and machine a slot down the middle for spring We are machining very complex thin aluminum parts with very thin windows. I am familiar with creating a stock model. not sure who made the video i just did a search online and stumbled on this one but it seems to show all the steps needed to create a stock model. There is a lot of topics on these forums on using stock models, this video here i found seems to show the process pretty well so hopefully the video below helps you get familiarized with stock models. Your best bet is to learn to use stock models. What am I missing to get these to work properly? Next step is starting the stock models from scratch on all the Ops and re orienting them and seeing if it will work a second time. I select the Pmesh as a "model" in the stock model and combined with the calculation time taking forever for just a few toolpaths it still comes in hollow(which doesn't even make sense to me). I tried File>save some then selecting it and saving as STL. But I cant select the Pmesh as stock in stock setup(for simulation).
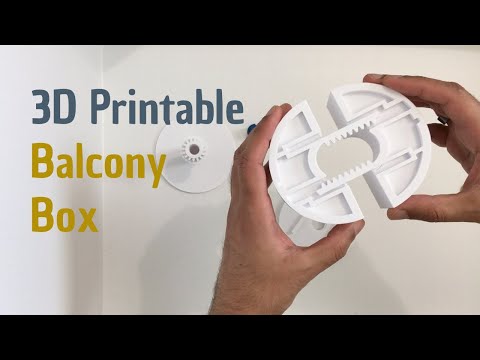
I have tried your suggestion as right click > mill toolpath > convert to pmesh. But now 160 programs deep on the 4th OP I am struggling with this. That method worked for me for the first few OPs. Says he has never had this issue in all of his years. Save the STL from the simulation, open the STL separately and orient it accordingly, resave it and use it in stock setup and in stock model. The guy training me has never seen or had this issue before so it is making me look even worse. I have a lot of experience with primarily with PowerMill and Tebis, but a little WorkNC and Gibbs and some of these simple issues are extremely frustrating. I just started at this company(and mastercam) 6 weeks ago. I'm currently having this problem too using 2018.
